SKETCHING
Typically, my initial sketches simply seek to understand the overall form in basic shapes and through orthographic and exploded views. As I begin to understand the ideal form 3-dimensionally, the lens become much more whimsical in nature.
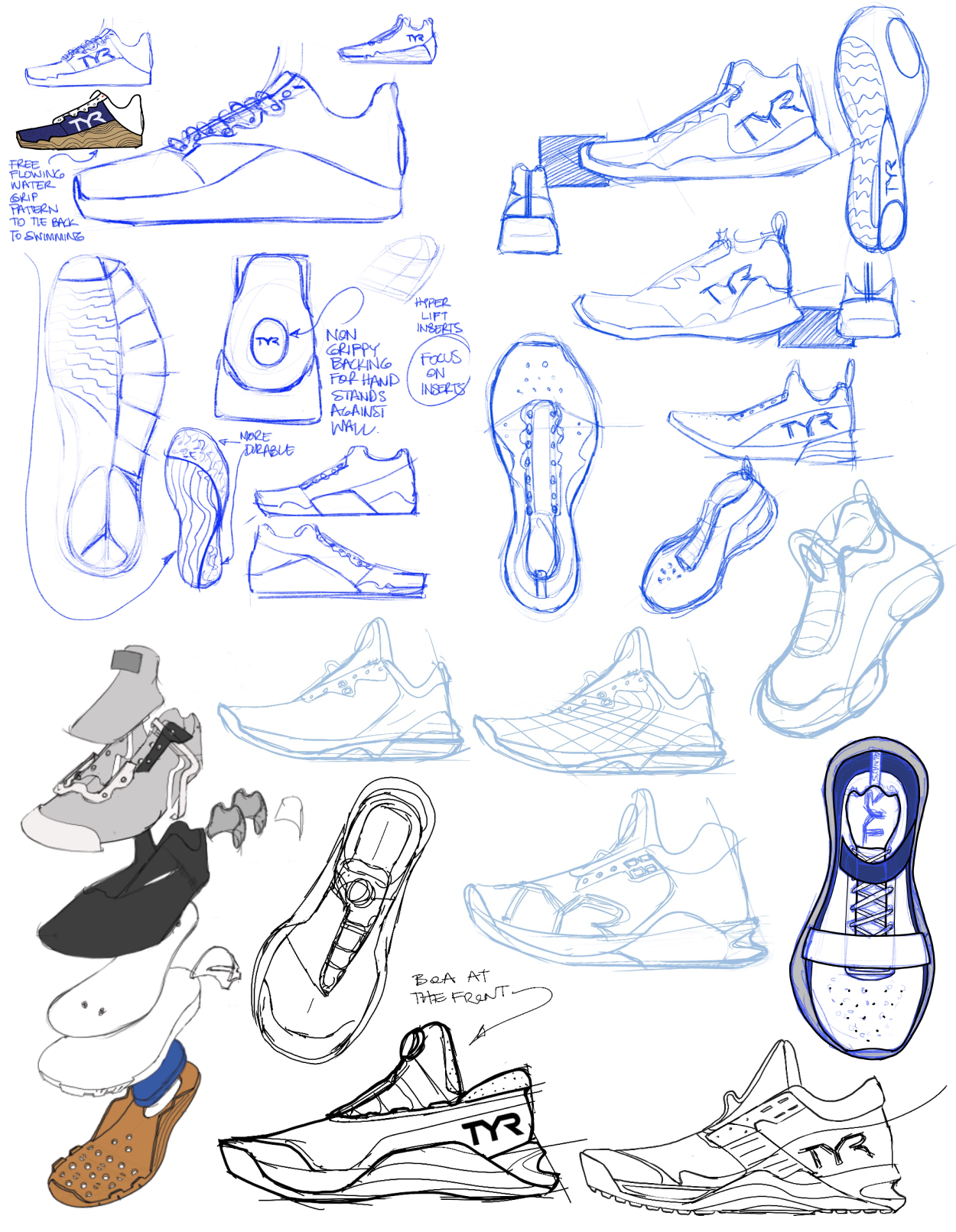
Following sketching, 2D designs are prepared for tech packs. Below is the final version of the 2D design following updates to initial samples, to more closely follow the shape of the approved model. After initial approvals, it was optimized for color updates for additional skus, which saved several work hours.
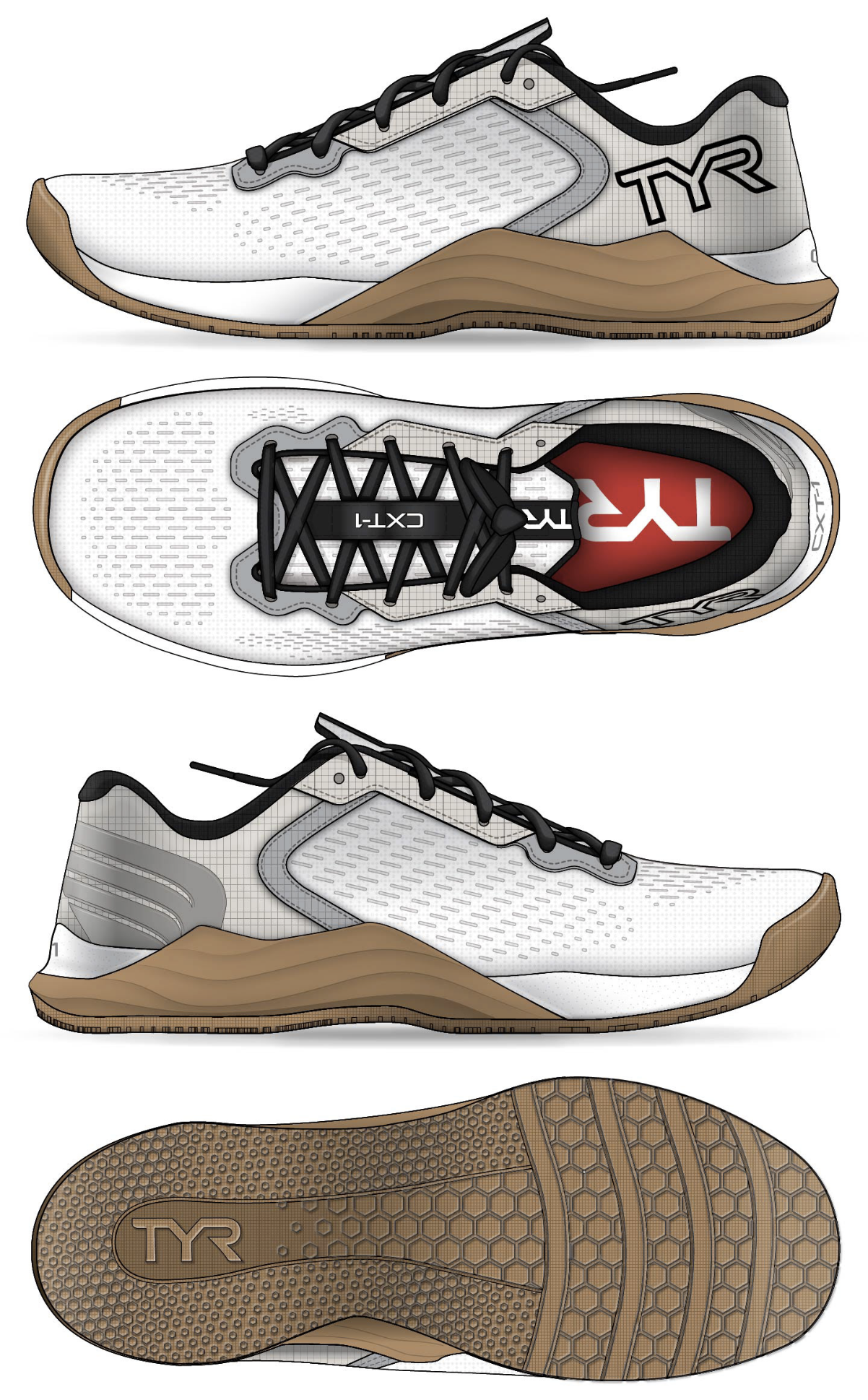
In addition, to ensure accurate design of the rubber outsole and minimize factory revisions, I modeled the side rail and sole in SolidWorks.
Documents for sourcing requests, initial and final techpacks, design updates, artwork alignments, and color requests were all used to measure correctness. Color correctness became most important for "standard" colors and colors that extended to other styles for them to sit as a family. Thinking ahead to how certain materials would take color and accounting for that was one strategy, as well as leaning on the factory to be more proactive in the quality control process. Clear directions and communication, despite language barriers was paramount.
Initially, there were several samples per style and after some fine tuning, standard brand colors typically only required one sample and only difficult colorways required more than one sample.
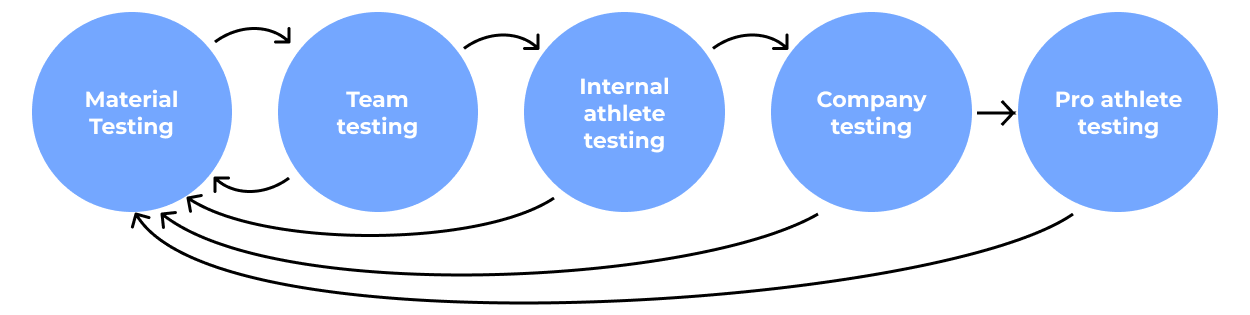
Frequent testing provided lots of feedback and data to make informed decisions and staggering the exposure based on the project stage allowed us to manage risk.
After approving designs and handing products off to the PM, I delivered technical copy for marketing to use on the web and reviewed their visual representations to ensure key features were accurately captured.